Prepress printing is a crucial stage in the printing process that bridges the gap between the design process and the actual production of printed materials. It involves preparing the design files and ensuring that they are optimized for printing. Prepress printing includes tasks such as checking the resolution and color mode of images, creating print-ready files, and setting up proper bleed and trim marks. The goal of prepress printing is to produce high-quality prints that accurately represent the original design. By following certain guidelines and best practices, businesses can ensure that their printed materials are visually appealing, professional, and error-free. In this article, we will discuss tips and techniques to produce quality prepress printing, from understanding color modes to optimizing file formats.
Planning the Design Process
A well-planned design process is crucial for achieving high-quality prepress printing results. By carefully considering the various aspects of the project, you can ensure that your final printed materials meet the desired specifications and expectations. Here are some tips to help you plan your design process effectively:
1. Design Brief: Start by creating a comprehensive design brief that outlines the main purpose of the design and the motivations of the client. This will serve as a roadmap throughout the project, guiding your decisions and ensuring that the final product aligns with the client’s vision.
2. Understanding Industry Terms: Familiarize yourself with key industry terms related to trimming, cutting, and shaping printed pieces. This includes understanding terms like bleed and margin. Bleed refers to when the design extends beyond the edge of the paper, requiring the printer to trim off any excess. A margin, on the other hand, is a blank space around the edge of the design to ensure that critical artwork or text is not cut off during trimming.
By including these terms in your design process, you can effectively communicate with printers and ensure that your design is executed exactly as intended.
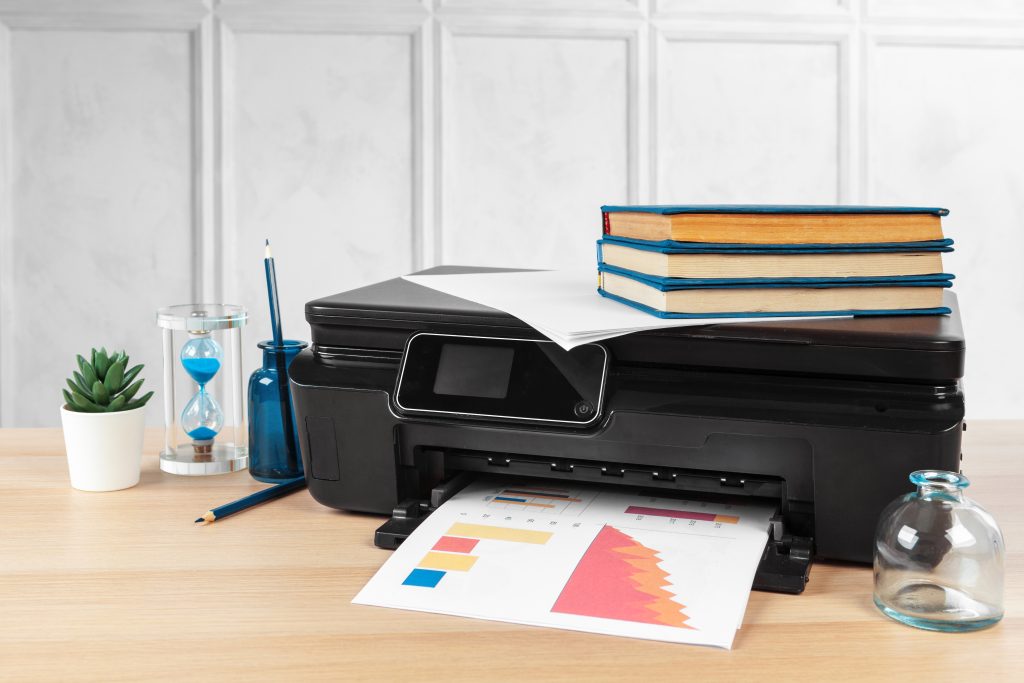
Preparing the Files for Prepress Printing
Preparing the files for prepress printing is a critical step in ensuring that your final printed materials meet the desired quality and specifications. Here are the necessary steps and considerations to follow:
1. Discuss printing needs with the commercial printer: It is essential to communicate your printing needs and requirements with the commercial printer. This includes discussing the desired paper type, printing method, quantity, and any specific instructions they may have.
2. Ensure correct file formats: Convert your design files into appropriate formats like PostScript or PDF. These formats are widely accepted in the printing industry and ensure that your designs are compatible with the printer’s software.
3. Determine color models: Choose the appropriate color model for your design. For most printed materials, the standard color model is CMYK (Cyan, Magenta, Yellow, Key/Black). However, if you have specific spot colors or brand guidelines, consider using spot colors. Avoid using RGB (Red, Green, Blue) color mode as it is primarily used for digital screens.
4. Address pre-press tasks: Before sending the final files to the printer, make sure to address any pre-press tasks. This includes checking the resolution of images (at least 300 DPI for print), embedding fonts, and converting text to outlines if possible. It’s also crucial to include trim marks and bleeds if your design extends beyond the edge of the paper.
By following these steps and considering these factors, you can ensure that your files are properly prepared for prepress printing, resulting in high-quality printed materials.
Understanding Color Separations, RGB Colors, & Additional Color Models
In the prepress printing stage, it is crucial to have a comprehensive understanding of color separations, RGB colors, and additional color models. These aspects play a significant role in ensuring high-quality print materials.
Color separations refer to the process of breaking down a design into separate color channels before printing. This is done to create plates for each color, typically Cyan, Magenta, Yellow, and Key/Black (CMYK), which are then used during the printing process. Color separations are essential as they allow for precise control over color reproduction, resulting in accurate and consistent prints.
RGB (Red, Green, Blue) colors are primarily used for digital screens and represent the colors achievable on devices like monitors and smartphones. In the printing industry, it is necessary to convert design files from RGB to CMYK color mode. RGB uses additive color mixing, while CMYK uses subtractive color mixing, which ensures better color accuracy in print. Converting files to CMYK is vital to avoid discrepancies between the displayed colors on screens and the final printed output.
Additionally, there are additional color models like Pantone spot colors that offer a wide range of specialized colors. Spot colors are pre-mixed inks that allow for precise color matching and consistency, making them ideal for branding, corporate logos, and specialized print projects. Spot colors ensure consistent color reproduction across different printing processes and materials.
Understanding color separations, RGB colors, and additional color models is essential for achieving high-quality prints. By considering these factors during the prepress stage, you can ensure accurate color reproduction and consistent results in your commercial printing projects.
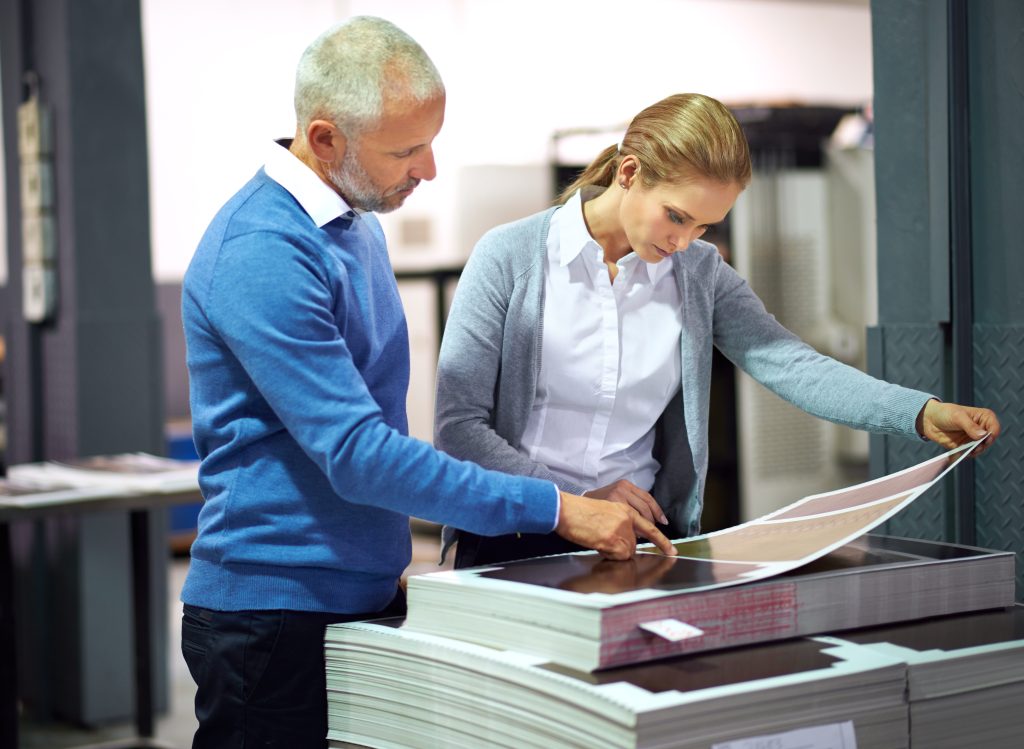
Conclusion
In conclusion, it is important to properly prepare your files for prepress printing. This includes ensuring correct file formats like PostScript or PDF, selecting the appropriate color model (usually CMYK), and addressing pre-press tasks like checking image resolution and embedding fonts. Additionally, gaining a comprehensive understanding of color separations, RGB colors, and additional color models is essential in achieving high-quality prints.
Average Rating