Prepress refers to the crucial phase of the printing process that takes place before a design is sent to the printing press. It involves a variety of tasks and processes to prepare the design files for production, ensuring that the final printed product meets the desired quality standards. This includes everything from the initial design process to the preparation of digital files, color separation, and the creation of printing plates. Prepress also involves activities such as proofreading and checking for errors, as well as optimizing color accuracy and consistency. The primary goal of prepress is to ensure that the design is translated accurately from the digital file to the final printed product, ensuring that the desired quality, colors, and details are maintained. With the right prepress tools and equipment, such as design programs like Adobe Creative Suite, advanced color management tools, and AI-powered color correction, the prepress phase plays a crucial role in achieving high-quality and visually appealing printed materials.
What are the Goals of Prepress?
Prepress is an essential part of the printing production process. Its primary objective is to prepare designs for printing by ensuring accuracy, optimizing color accuracy, and enhancing efficiency.
The importance of prepress cannot be overstated. It acts as the bridge between graphic design and the final printed product. It involves various tasks such as creating accurate proofs, color separation, and preparing digital files for printing plates.
The goals of prepress are multifaceted. Firstly, it aims to create accurate proofs that closely resemble the final printed product. It ensures that the colors, images, and layout are correct before sending the design for printing. This step not only saves time and money but also helps avoid potential errors or reprints.
Secondly, prepress focuses on optimizing color accuracy. Each printing process has its unique color gamut, and prepress helps achieve the desired color tones and spot colors. It involves color corrections, color separations, and advanced color management tools to ensure consistency and quality throughout the print run.
Moreover, prepress aims to ensure proper file preparation. It involves checking for resolution, bleeds, and other technical specifications to avoid issues during printing. Addressing file preparation concerns in the prepress stage, streamlines the printing process, saving time and preventing errors.
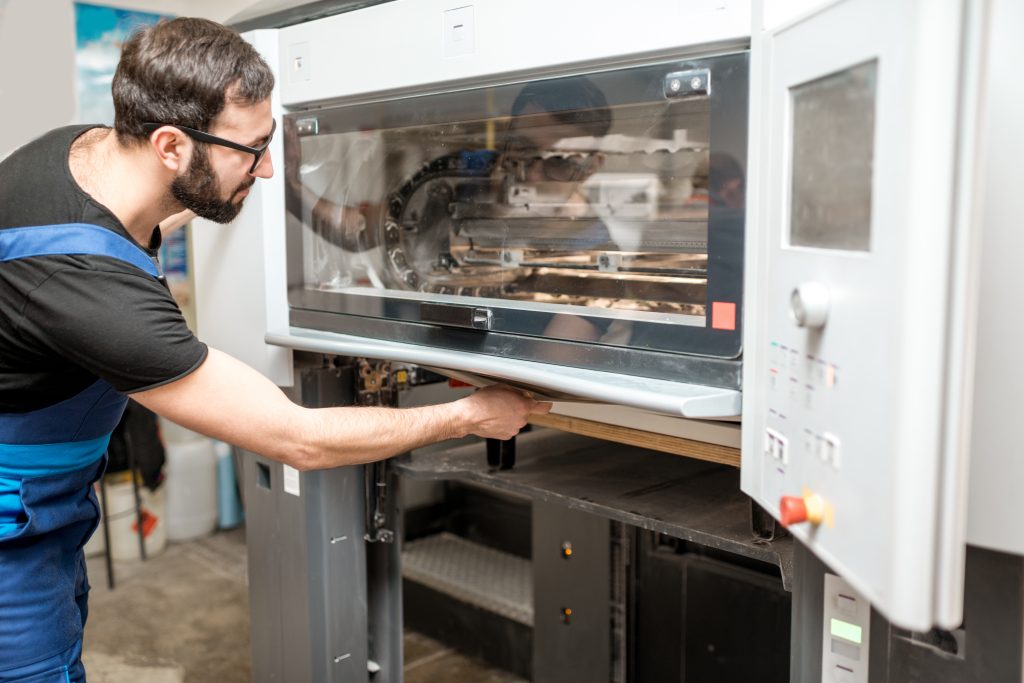
Types of Prepress Equipment and Tools
Prepress requires a range of specialized equipment and tools to carry out its tasks effectively. These tools enable prepress technicians to accurately prepare designs for printing, optimize color accuracy, and ensure efficient workflow. Some of the common types of prepress equipment and tools include light tables, design programs such as Adobe Creative Suite, digital proofing systems, color separation tools, and advanced color management tools. Light tables are used for inspecting physical prototypes, negative films, and print test sheets, allowing technicians to identify any issues like air pockets or color discrepancies. Design programs like Adobe Creative Suite provide a platform for creating and editing design files, allowing technicians to make necessary adjustments before sending them for printing. Digital proofing systems help create accurate proofs that closely resemble the final printed product, facilitating quality control. Color separation tools aid in the process of separating different colors for printing, while advanced color management tools ensure color accuracy and consistency throughout the print run. With the right equipment and tools, prepress technicians can effectively carry out their tasks, resulting in high-quality printed materials.
Light Table
A light table is a crucial tool in the prepress production process. It is a flat, illuminated surface that allows for the examination and manipulation of printed materials and negatives. The importance of lamp intensity cannot be overstated when producing consistent photopolymer printing plates. The intensity of the light determines the quality and clarity of the images being viewed, ensuring accurate reproduction during the printing process.
In addition to lamp intensity, measuring plate relief is essential in maintaining print quality. Prepress technicians use specialized tools like digital plate micrometers to measure the depth of the plate relief, ensuring that the print will transfer correctly onto the substrate. Accurate measurement is necessary to avoid issues such as under-inking or excessive dot gain, which can affect the quality of the final printed product.
Overall, light tables play a vital role in the prepress workflow, allowing for careful examination and manipulation of materials. They ensure that the printing process runs smoothly by providing accurate visuals for inspection and precise measurement of plate relief. By utilizing the right equipment and tools, prepress technicians can produce high-quality printing plates, leading to impeccable finished products.
Flexographic Printing Processes
Flexographic printing processes are commonly used in prepress production for various applications, including label designs and packaging materials. This type of printing works by transferring ink onto the substrate using flexible relief plates.
Flexographic printing offers several benefits, making it a popular choice in the industry. First, it allows for faster printing speeds compared to other methods, increasing productivity and efficiency. Additionally, the print quality is consistently high, ensuring sharp and clear images. Flexographic printing also supports the use of a wide range of materials, from plastic to paper, making it versatile for different printing requirements.
To carry out flexographic printing, certain tools and equipment are necessary. These include flexographic printing presses, which are specifically designed for this printing process. Anilox rolls and doctor blades are used to control the amount of ink transferred onto the plate and ensure precise ink metering. Flexible relief plates, made of rubber or photopolymer material, are crucial for creating the desired image or text. Other tools such as plate-mounting tape, plate cleaners, and plate drying ovens are also essential for maintaining the quality and durability of the plates.
Digital Printing Plates
In prepress production, digital printing plates play a crucial role in ensuring high-quality prints and efficient printing processes. These plates are used to transfer the image or design onto the printing surface.
Digital printing plates offer several advantages over traditional methods. Firstly, they allow for faster turnaround times. Unlike conventional offset printing plates, which require time-consuming steps such as exposure and chemical processing, digital plates offer instant imaging capabilities. This means that printing plates can be created and ready for use in a fraction of the time, reducing production time and enabling quicker delivery of prints.
Another key advantage of digital printing plates is their ability to facilitate personalized prints. With digital technology, it is possible to easily modify the image or design, allowing for customization and variability in prints. This is particularly beneficial for marketing purposes where targeted messaging or personalized communications are required.
Furthermore, digital printing plates are cost-effective and flexible. Unlike offset printing plates that require large print runs to be economical, digital plates can produce high-quality prints in lower quantities. This makes digital printing plates suitable for small print jobs or print-on-demand services. Additionally, digital plates can be easily stored and reused, minimizing waste and reducing costs.
Digital Files and Finished Products
In the prepress stage, digital file preparation is a crucial step in ensuring high-quality printing and the production of finished products. This process involves converting designs, graphics, and text into digital files that are suitable for printing.
One important consideration in digital file preparation is selecting the appropriate file format. Common file formats for print include PDF, EPS, and TIFF. These formats preserve the quality and integrity of the design elements, ensuring a crisp and accurate reproduction of the finished product. Additionally, choosing the correct resolution is vital for achieving sharp and detailed prints. The recommended resolution for printing is typically 300 dots per inch (DPI) to ensure the highest level of clarity and sharpness.
Digital printing offers numerous advantages, including the ability to print lower volumes and customized publications. Unlike traditional offset printing, which requires large print runs to be economical, digital printing allows for smaller print quantities, making it cost-effective for small businesses and personalized marketing campaigns. Digital printing also enables variable data printing, which allows for customization on a mass scale, such as adding unique information to each printed piece.
Another advantage of digital printing is the use of toner or inkjet cartridges. Digital printers utilize these cartridges to apply ink onto the printing surface. This allows for precise and consistent color reproduction, resulting in vibrant and accurate prints.
Advanced digital printing machines also offer options for additional spot colors and special inks. Spot colors refer to specific premixed ink colors that are used to achieve precise shades or unique effects. These colors can be added to the printing process to enhance the overall appearance and impact of the finished product. Special inks, such as metallic or fluorescent inks, can also be utilized to create eye-catching and visually appealing prints.
Preparing for Prepress Production
Preparing for prepress production involves a variety of tools and equipment to ensure that the digital files are ready for printing. One essential tool is prepress workflow software, which helps streamline the prepress tasks and ensures a smooth transition from the design process to the print process. This software allows for efficient file management, color management, and imposition planning. Additionally, prepress technicians rely on tools such as a light table, which is used to inspect and verify the quality and accuracy of printed materials by examining physical prototypes or test sheets. Other necessary equipment includes high-quality scanners for capturing physical designs and converting them into digital files, as well as printing plates and prepress molds for different printing methods. Prepress technicians also use advanced color management tools, such as AI-powered color correction, to ensure color accuracy and consistency throughout the printing process. Overall, the proper tools and equipment are vital in achieving high-quality prints and meeting the industry’s quality standards in the prepress process.
Designing a Label or Other Printed Material
Designing a label or other printed material involves several steps to ensure the final product meets the requirements. The first step is to gather all the necessary information and specifications for the project. This includes understanding the target audience, the purpose of the label, and any specific branding or design guidelines.
Once the initial information has been gathered, the next step is to create the design. This involves utilizing design programs such as Adobe Creative Suite to develop the layout, typography, and graphical elements of the label. Various design techniques such as color management, spot colors, and color tones are incorporated to achieve the desired look.
After the design has been finalized, dielines are created. These are the templates that indicate the exact dimensions and shapes of the label or printed material. Dielines are crucial for ensuring the artwork aligns correctly during the printing process. They also help in determining the placement of graphics, text, and any additional elements such as barcodes or QR codes.
Once the deadlines are established, digital proofs are generated. Digital proofs, which are digital representations of the final product, allow for a comprehensive review of different aspects, such as color accuracy, design elements, and overall composition. These proofs act as a virtual sample, offering a preview of how the label will look when printed.
To further evaluate the design and functionality, physical prototypes are produced. These prototypes provide a tactile experience and allow for a more detailed review of elements such as material selection, texture, and finish. Prototypes help identify any issues or improvements needed before mass production, ensuring that the final product meets the necessary quality standards.
Through the use of deadlines, digital proofs, and physical prototypes, designers and clients can review and evaluate various aspects of the label or printed material. This iterative process allows for necessary adjustments, approvals, and finalization of the design, leading to a high-quality, visually appealing, and functional end product.
Design Programs Used in Prepress Production
Design programs play a vital role in prepress production by enabling the creation and preparation of print-ready files. One of the most popular design programs used in prepress is Adobe Creative Suite. This suite of software includes Adobe Photoshop, Illustrator, and InDesign, each offering unique features and benefits.
Adobe Photoshop is widely used for image manipulation and color adjustments. It allows prepress technicians to enhance and optimize images, adjust color tones, and remove imperfections. This ensures that the final printed output reproduces accurate and vibrant colors.
Adobe Illustrator is commonly utilized for creating vector-based graphics and illustrations. It is ideal for designing logos, icons, and typography that can be scaled seamlessly without losing quality. In prepress, Illustrator is used to create clean and precise deadlines, ensuring accurate alignment and dimensions.
Adobe InDesign is a layout program that brings together elements created in Photoshop and Illustrator. It is used to arrange graphics, text, and images into a cohesive design. In prepress, InDesign is crucial for creating multi-page documents and preparing them for printing.
These design programs streamline the prepress process by offering comprehensive tools for color adjustments, file preparation, and creating proofs. They allow prepress technicians to work efficiently, ensuring high-quality printing and accurate reproductions of colors and design elements.
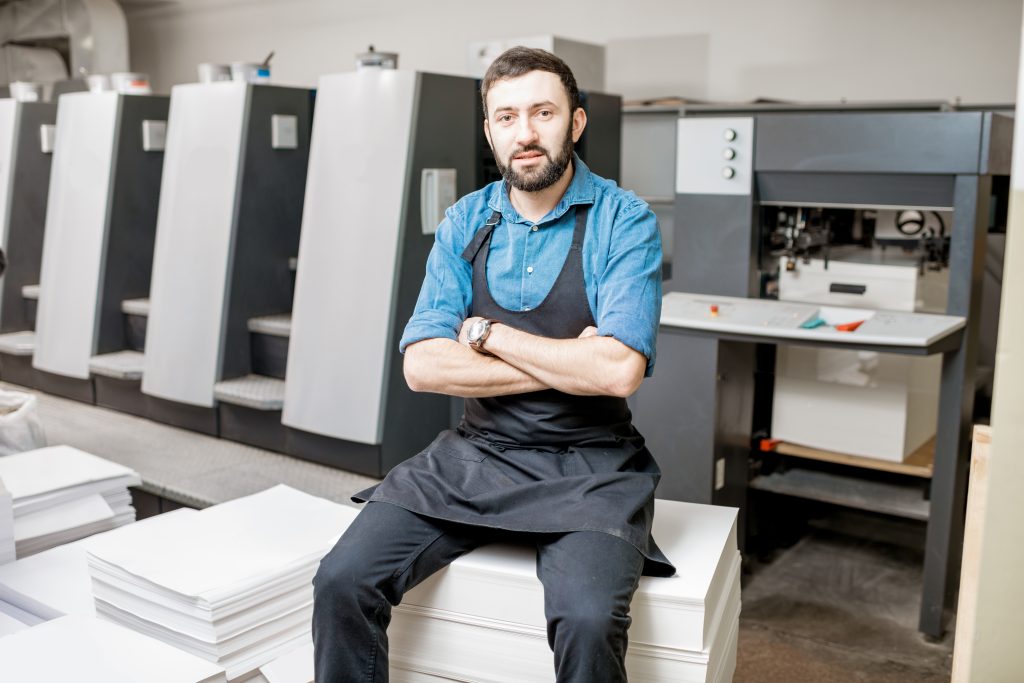
Conclusion
In conclusion, final proofing is a vital step in the pre-press production process. By following best practices such as using test sheets, reviewing prints under different lighting conditions, and checking for prepress errors, prepress technicians can guarantee the accuracy and quality of the final prints.
Average Rating